An ERP for Mining Processes - the missing link in Mining's Digital Transformation
- minerp
- Jul 7, 2022
- 4 min read
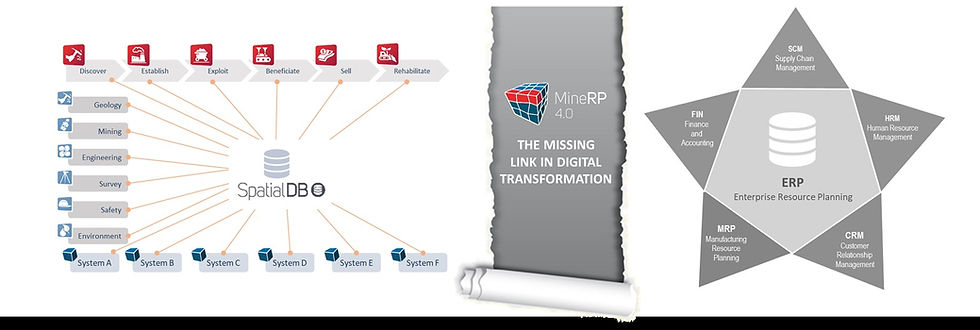
Mining has been trailing Manufacturing in the digitalization trend, and one of the main reasons for that has been the data divide between Mining's Technical and Commercial Systems. This divide makes it impossible for mines to be managed like factories. In this blog I will explore this stumbling block to digitalization and describe how we at MineRP went about bridging the divide with our MineRP 4.0 Enterprise Integration Platform.
Research Studies suggest that the integration gap in the mining sector can create a productivity loss of about 10%-20%. Paul Mithchell
In a factory, Enterprise Resource Planning (ERP) software integrates all of the data from manufacturing, its support processes and the financial system into a central, logical relational database, in real time. This enables the factory to plan and manage its inventory and production processes as well as its finances and support services, in an integrated system. To duplicate this in a mine, the Mine Technical Systems (MTS) that account for the available ore reserves (the inventory in a factory) has to integrate with the systems that enable and manage the mining process (the manufacturing process) as well as the systems that for the support functions like HR, Health and Safety etc.
An added complication is the fact that, unlike in a factory, infrastructure development and production runs concurrently in a mine for most of its life. This adds the need for integration with the systems that enable the civil engineering processes that "builds the factory".
The Digital Mine aspires to Integrated Business Planning, where the master production schedule (mining and its supporting processes) is fully integrated with the commercial (human resources, financial) schedules. However, ERP solutions implemented in mining only address the commercial schedules, and are unable to completely integrate the production and commercial domains.
All of the data needed to model the ore resource and run a mining operation is created in expert applications (513 apps and 268 vendors at the last count), with data typically stored in proprietary databases and file formats.
In his article- The Open Mining Format is more important than you think. Industry 4.0. Adrian Large describes the problem we have in the mining industry with proprietary file formats and calls for the adoption of a universal format in which 3D models can be stored to be adopted by the vendors. "3D models are the very foundation upon which ore deposits are interpreted, mines are operated, planned, and scheduled. The role of the 3D model and its inability to be interoperable between software packages is an obstruction too big to ignore."
3D models are the very foundation upon which ore deposits are interpreted, mines are operated, planned, and scheduled. The role of the 3D model and its inability to be interoperable between software packages is an obstruction too big to ignore.
We at MineRP realized in 2004 there was an opportunity to create an ERP for mining processes, if we could solve the interoperability problem between mine technical systems. We also realized that this interoperability would never occur organically, since there is no incentive for Vendors to Standardize their file format "who use their proprietary file format as a way of securing users". We embarked on the development of a spatial database for mining to act as a central standardized repository and translation layer for all data created by the various expert applications.
In a spatial database, data is related (indexed) according to its coordinates (position) in space as well as time. Although certain GIS vendors already had their own spatial databases no-one had a mining specific 3D-database. The advent of Microsoft SQL 2005 that supports spatial geometries, placed us at MineRP in the position to build our own spatial database, dubbed MineRP SpatialDB. We did this by creating a spatial extension library on top of MS SQL server, and included extended mining logic and enriched the database management system.
In the Mining Industry, key information is captured and represented in 2D and 3D CAD systems forming the basis for planning and the management of the execution of the plan. For example, a physical mining panel and/or a blasting block is represented by a 3D block or volume. The block has specific line thickness, hatching, and colors to identify it. Text and symbols around the CAD drawing convey information about the drawing e.g. blasting date. The challenge to MineRP was to unpack CAD drawings, the features and related metadata (unstructured data) into the Spatial Database, i.e. give structure to the data.
The robustness of MineRP SpatialDB lies in:
Amalgamating the data created in the expert applications; in other word we translate every bit and every bite into our spatial database. This is very important because traditionally only the data needed for use in the next application is transferred. This gave rise to data attrition along the value chain. For example, by providing only a block model to the scheduling engine the context of the geological model is often lost.
Creating a receiving environment to enforce the rules for data storage, naming conventions and how elements are described in the Spatial Database. (Referred to as an Inbound Book of Standards). Thus giving structure to unstructured data with a fully implemented Meta Data Register (MDR).
Making all mining geometries fully spatially aware in a standardized format by subscribing to the Open Geospatial Consortium (OGC)'s Simple Features for SQL standard, which we extended with mining logic.
Central configuration, administration, security and data management of all enterprise spatial data
In order to build a mine technical ERP we created MineRP 4.0

A Spatial Data Infrastructure (SDI) centred on our spatial database, thereby adding functionality that enable:
Interoperability between expert systems (MineRP 4.0 is source-data agnostic),
Rapid parametric Mine Design and Sequencing,
Enterprise Scheduling,
Ease of access of data for reporting and analysis,
Visual representation of data in 2D and 3D contextualizing information by integrating datasets from various source systems,
Workflow orchestration triggered by business rules and
Data sharing between MineRP 4.0 and commercial ERP's
In short, MineRP 4.0 is a unique mine technical enterprise integration platform that bridges the gap between mine technical and commercial ERP systems. MineRP 4.0 leads the way for mines that want to digitalize across the value chain, because of its ability to amalgamate spatial data from disparate mine technical systems enabling integrated planning through data mediation platforms with commercial ERP systems.
Comments